How to add manufacturing parameters
Introduction
When using the ColdStream platform for detailed designs, the generative design tool will create a manufacturable design. By doing so, you can push the limits of your design towards the limit of your manufacturing technique. The manufacturing settings can be managed through the libraries page. In the table below you can find a summary of the supported manufacturing techniques and their relevant parameters.
CNC milling
Parameter | Unit | Explanation | Required |
---|---|---|---|
| | This parameters governs the solid structure width | The user is required to provide a lower limit for the structure width |
| | This parameters represents the milling tool and thus governs the channel width. This parameter also puts a limit on the inner curvature radius of structures | The user is required to provide a lower limit for the channel width |
| | This parameter limits how deep the milling tool can operate | Yes |
| The orientation gives the user control in which direction the milling tool operates:
|
Yes |
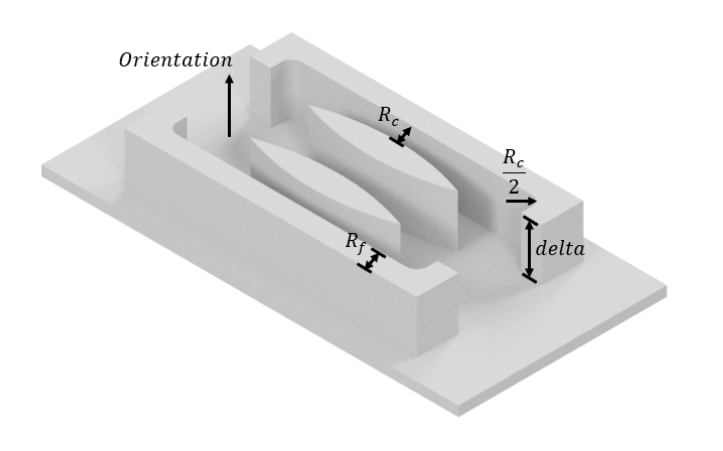
Planar CNC milling parameters
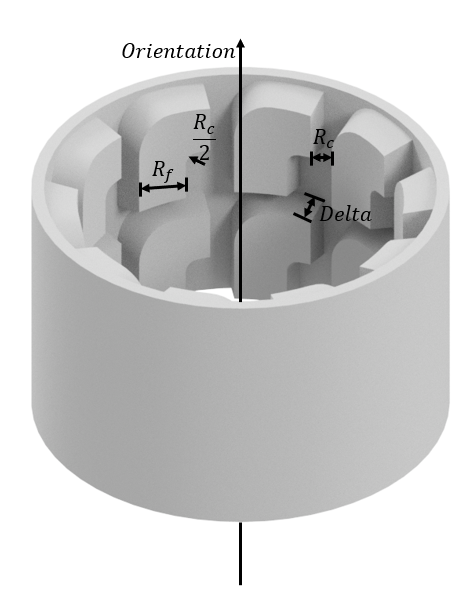
Radial CNC milling parameters
Important
The design region should be hollow in order to use radial CNC milling.
Die casting
Parameter | Unit | Explanation | Required |
---|---|---|---|
| | This parameters governs the solid structure width measured at the tip excluding the fillets. | The user is required to provide both a lower and an upper limit. |
| | This parameters governs the the minimal curvature radius of the solid structures. If no value was given, the default is set to the minimal structure width divided by 2. | No |
| | This parameter gives users control over the channel width between solid structures. If no lower or upper limits are provided, the default is set to the structure widths. | No |
| | This parameter governs what fillet is added at the root of the structures. | Yes |
| | This parameter governs what fillet is added at the tip of the structures. | Yes |
| | The draft angle of the fins. | Yes |
| | The maximum height of the cooling structures. | Yes |
| The orientation gives users control in which directions the cooling structures are generated | Yes |
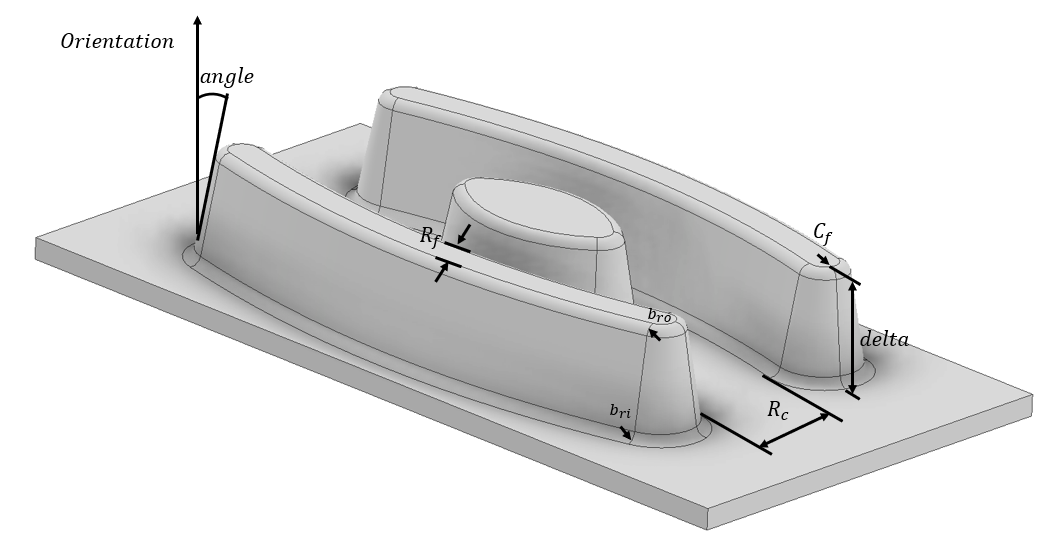
Die casting parameters
3D printing
Parameter | Unit | Explanation | Required |
---|---|---|---|
| | This parameter describes how thick the structures can be. | A lower limit is required |
| | This parameter describes channel width between printed structures. | A lower limit is required |
| | The maximum allowed overhang angle. This property is set by default to 45°. | No |
| | The maximum allowed unsupported cantilever length. This property is set by default to 2 millimeter. | No |
| | The maximum allowed unsupported bridgeable length. This property is set by default to 4 millimeter. | No |
| The orientation axis dictates in what direction the structures are manufactured. | Yes |
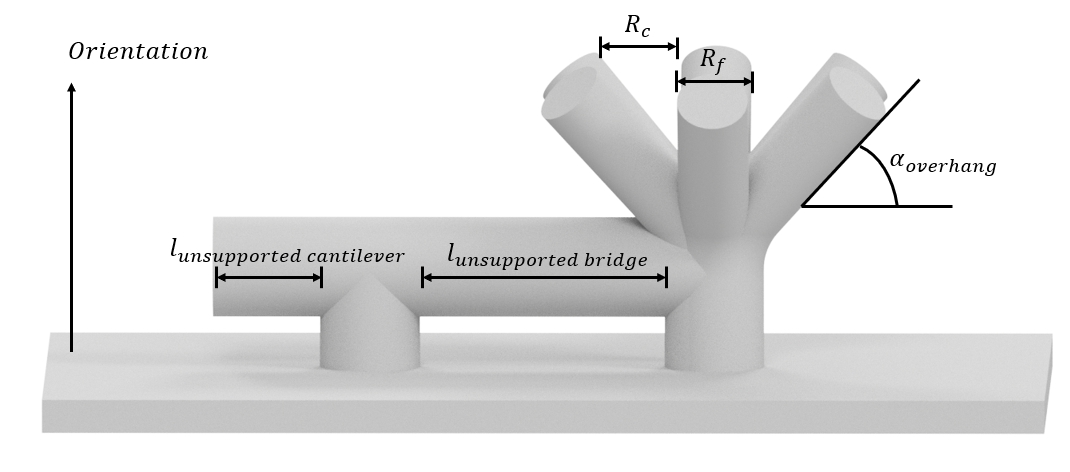
3D printing parameters
Sheet metal forming
Parameter | Unit | Explanation | Required |
---|---|---|---|
| | This parameter governs how wide the added structers can be. If no parameters are provided, the structure width will be identical to the channel width. | No |
| | This parameter puts a lower limit on the curvature radius of the structures. If no parameter is specified, the curvature radius is equal to the minimal structure width divided by 2. | No |
| | This parameter governs how wide the channels can be. | The user is required to provide both a lower and an upper limit. |
| | This parameter specifies what fillet radius should be added at the root of the structures and is measured on the inside of the bend. | Yes |
| | This parameter specifies what fillet radius should be added at the tip of the structures and is measured on the inside of the bend. | Yes |
| | The thickness of the stamped plate. | Yes |
| | The chamfer angle of the channels. | Yes |
| | The height of the fluid region. | Yes |
| The normal of the stamped plate. | Yes |
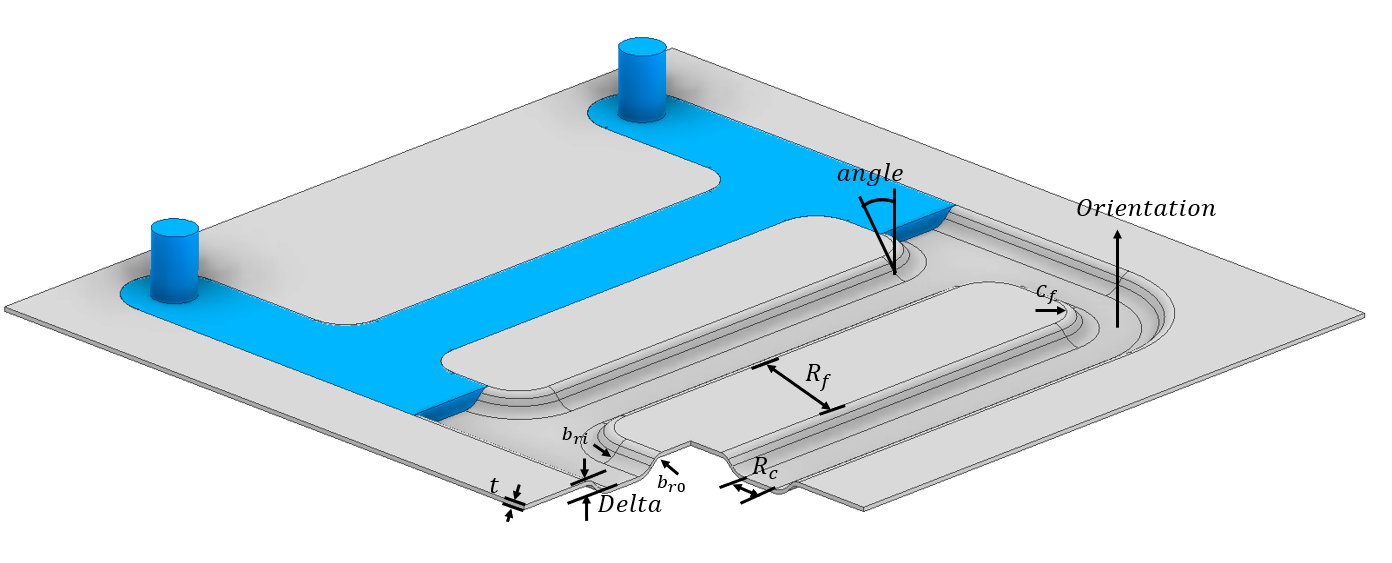
Sheet metal parameters
Important
The design region for sheet metal formed cases should be tall enough for both the fluid channels as well as the plate thickness! The design region height should thus be equal to the sum of channel height (delta) and the plate thickness (t). The fluid domain should locally be increased in height with the plate thickness (t) wherever there is a design domain.
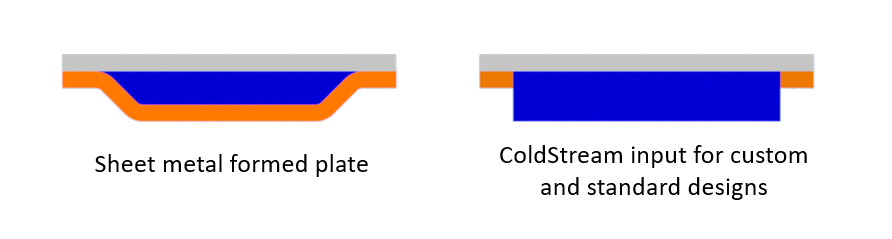
Slice view of the final sheet metal formed design on the left and what ColdStream expects as input on the right.
Electric wire generation
Parameter | Unit | Explanation | Required |
---|---|---|---|
| | The diameter of the generated electric wire. | Yes |
| | The minimal curvature radius of the generated electric wire. If no value is specified, the default is set to the wire diameter. | No |
| | The minimal spacing between different sections of the generated electric wire. If no value is specified, the default is set to the wire diameter. | No |
- represents the generated power in watts .
- represents the voltage on the wire in volts .
- represents the resistivity of the material used in ohm times meter .
- is the length of the wire in meters , which has an upper limit based on the size of the design domain.
- is the radius of the electric wire in meters .
This manufacturing technique is very different from the other ones. The design region that will come out of this optimization will have a heat source due to the Joule heating.
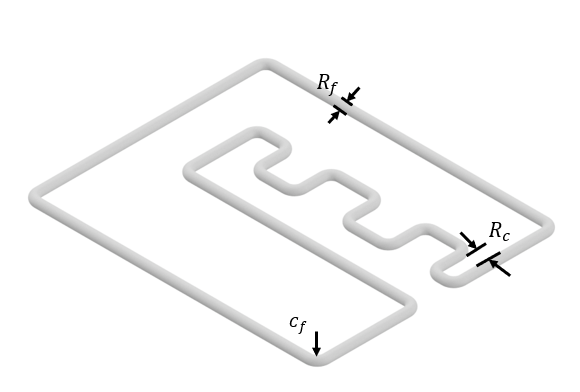
Electric wire parameters
How to select the appropriate manufacturing setting for your design case setup?
The manufacturing type needs to be selected when setting up the design region. After selecting the manufacturing method, you need to select the manufacturing parameters. This can be a predefined set of parameters or you can add a new set of parameters to the libraries.
Important
Note that an orientation should be specified. It is very important to look at the orientation of your model and make sure that the right orientation axis is selected!
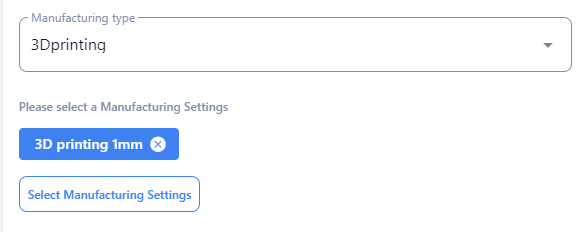
Select manufacturing settings in the design subregion setting window
How to add a new set of manufacturing parameters?
To enter a new set of manufacturing parameters, you need to go to the libraries and enter the manufacturing section. Here you can add a new set of parameters by clicking the add settings button.
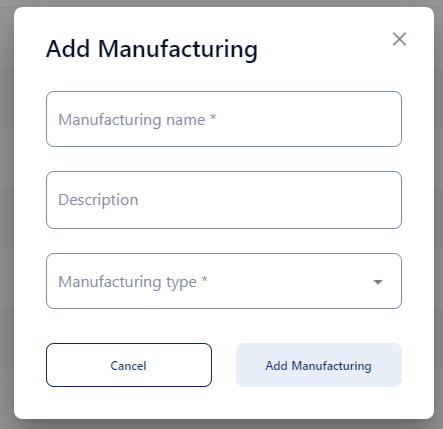
Add a set of manufacturing parameters.
Updated 7 months ago