Physics
Introduction
This page details which physical phenomena are included and how you as a user can influence them. Please navigate to the phenomenon you are interested in to learn more about it.
Heat sources
Introduction
A source is where heat enters your case. On ColdStream there are two types of sources: indirect sources and direct sources. Direct sources are controlled by the user during the case setup. A user can specify this heat input during the case setup. On the other hand, indirect sources are unaffected by the user during the case setup. For example, viscous dissipation in the fluid region(s) will always be activated when a case is running.
This article focuses solely on how you can correctly use direct sources on ColdStream.
User input | Unaffected by user | |
---|---|---|
Direct source | Yes | |
Indirect source | Yes |
What are direct sources
Direct sources are heat inputs specified directly by the user during the case setup. These sources are due to Joule heating, chemical reactions, or some other phenomenon.
This quantity of heat is spread out evenly over the entity on which it is defined, meaning that:
- if the heat input is specified on a surface patch: the local heat map is uniform:
Where is the area of the surface patch.
- if the heat input is specified on a (sub)region: the volumetric heat map is uniform:
Where is the volume of the (sub)region.
If the input value is negative, the heat source becomes a heat sink. This means that instead of heat entering through that entity, it leaves through that entity.
Important
The specified quantity of heat is spread out uniformly over the entity on which it is defined.
How to use direct sources?
As stated earlier, direct sources are specified by the user during the case setup. A user has the choice to include a heat source for all entities (regions, subregions, and surface patches) available in the geometry. The following subsections go into more depth on how to assign these heat sources for each of the entities individually.
Direct sources on regions and subregions
During the case setup, all regions (not including the subregions) have an input field for a heat source (Q). By default it is set to 0, meaning no heat is entering or leaving through it. Fill in the required value if you want to overwrite that default value.
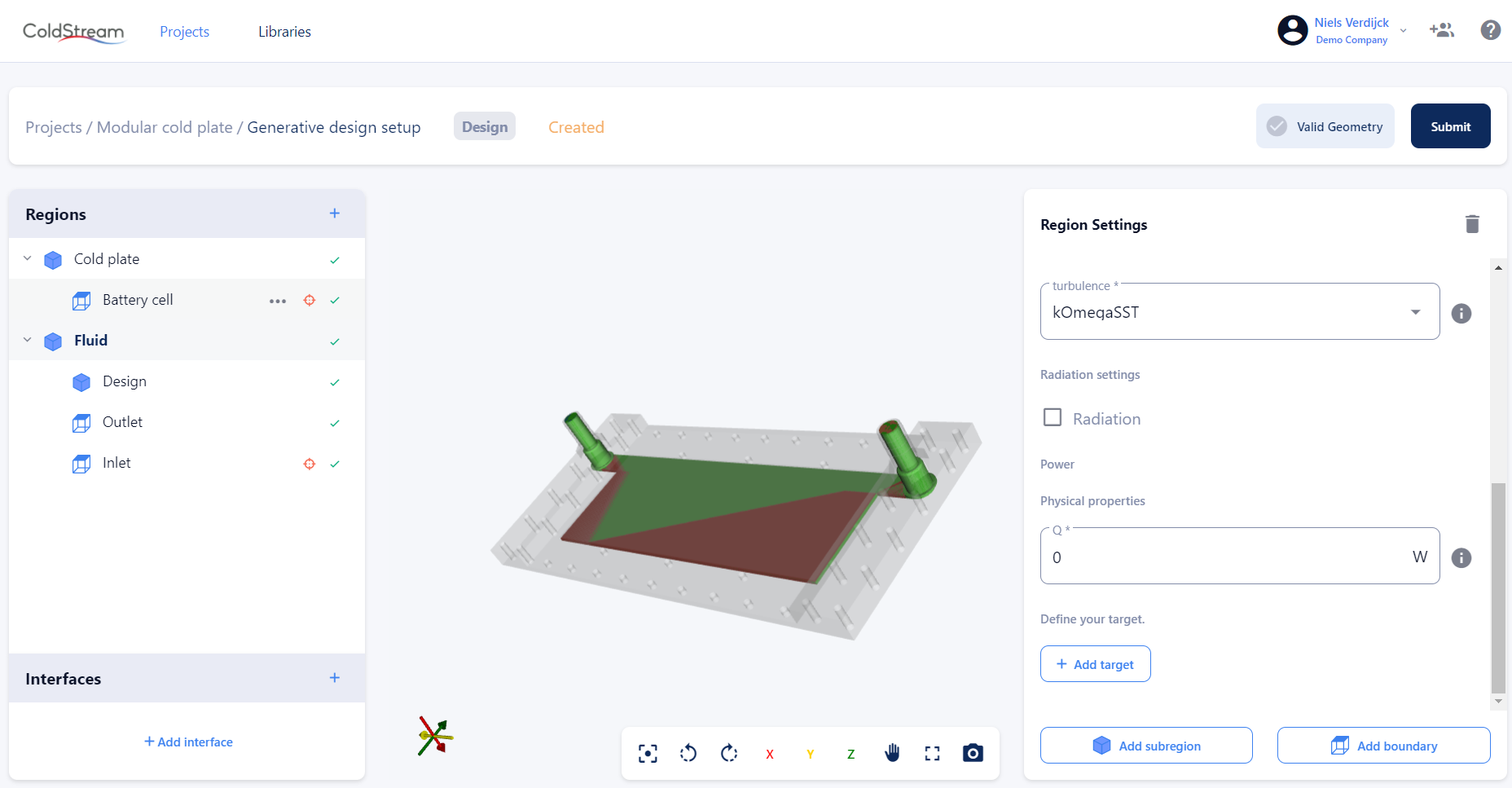
Heat source input field for a region
As stated in the previous section, the inputted value is distributed uniformly over the entire volume. In case you want a more localized heat production, you can include a subregion. This subregion must be of type 'general', not of type 'design'.
The heat source input field is identical to the one of a parent region. However, the heat is now distributed uniformly in that subregion only, not in the entire parent region. You can include as many subregions as you like, as long as they don't overlap. Be warned though, that the more regions you include, the longer it will take for the platform to complete your case.
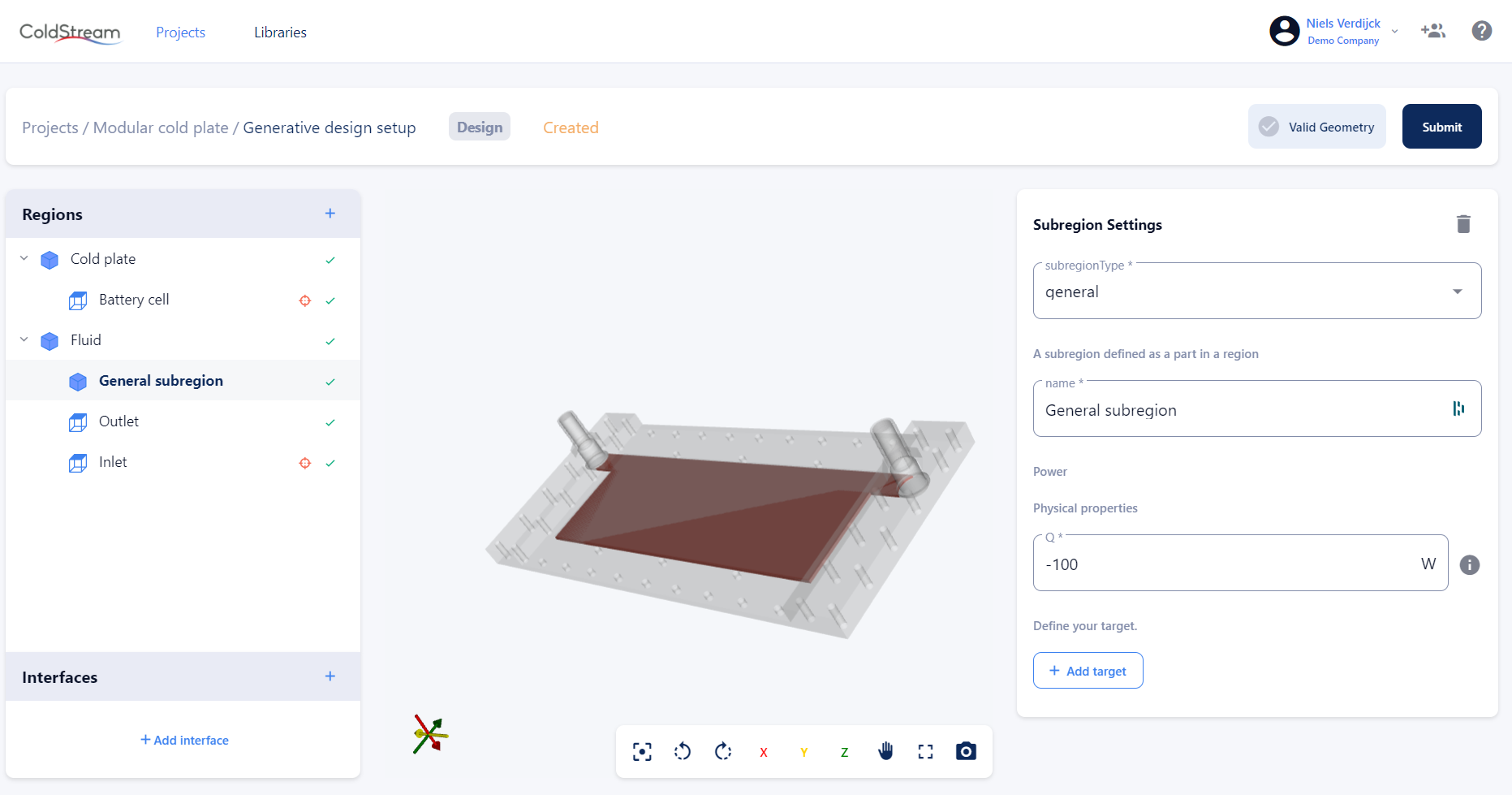
Heat source input field for subregions of type 'general'
Direct sources on surface patches
There are only two types of surface boundary conditions that allow you to specify a direct heat source. These are the heatedWall boundary condition and the insulatedWall boundary condition.
The heatedWall boundary has the same heat source input field as the regions and subregions have. The inputted value will be distributed uniformly over the entire area of this surface patch.
An insulatedWall does not allow any heat to be transferred through it. This means that you explicitly tell ColdStream that heat can't enter or leave this surface patch. An insulatedWall is also assumed wherever a region does not have an interface with another region.
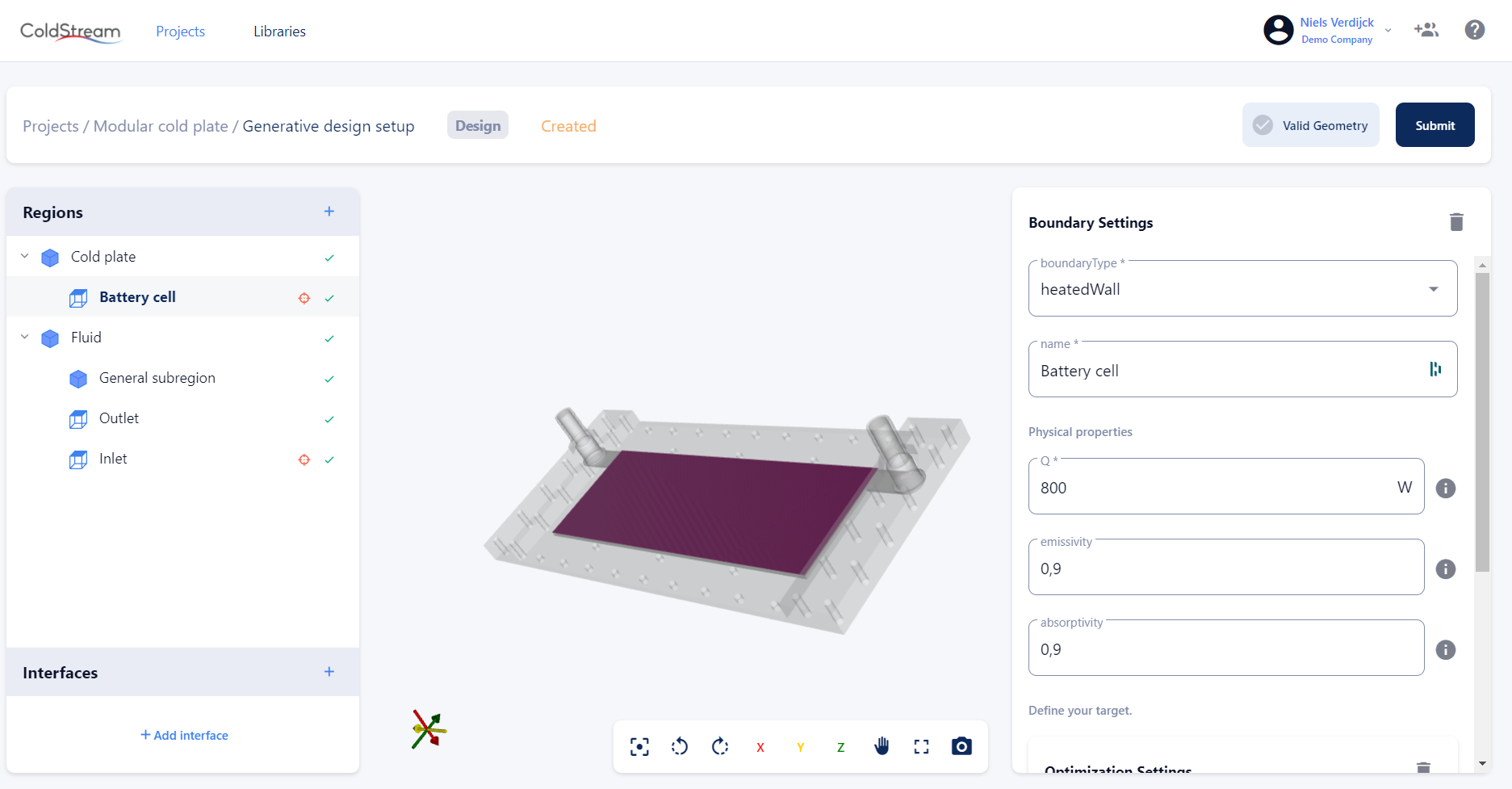
Heat source input field for heatedWall boundary
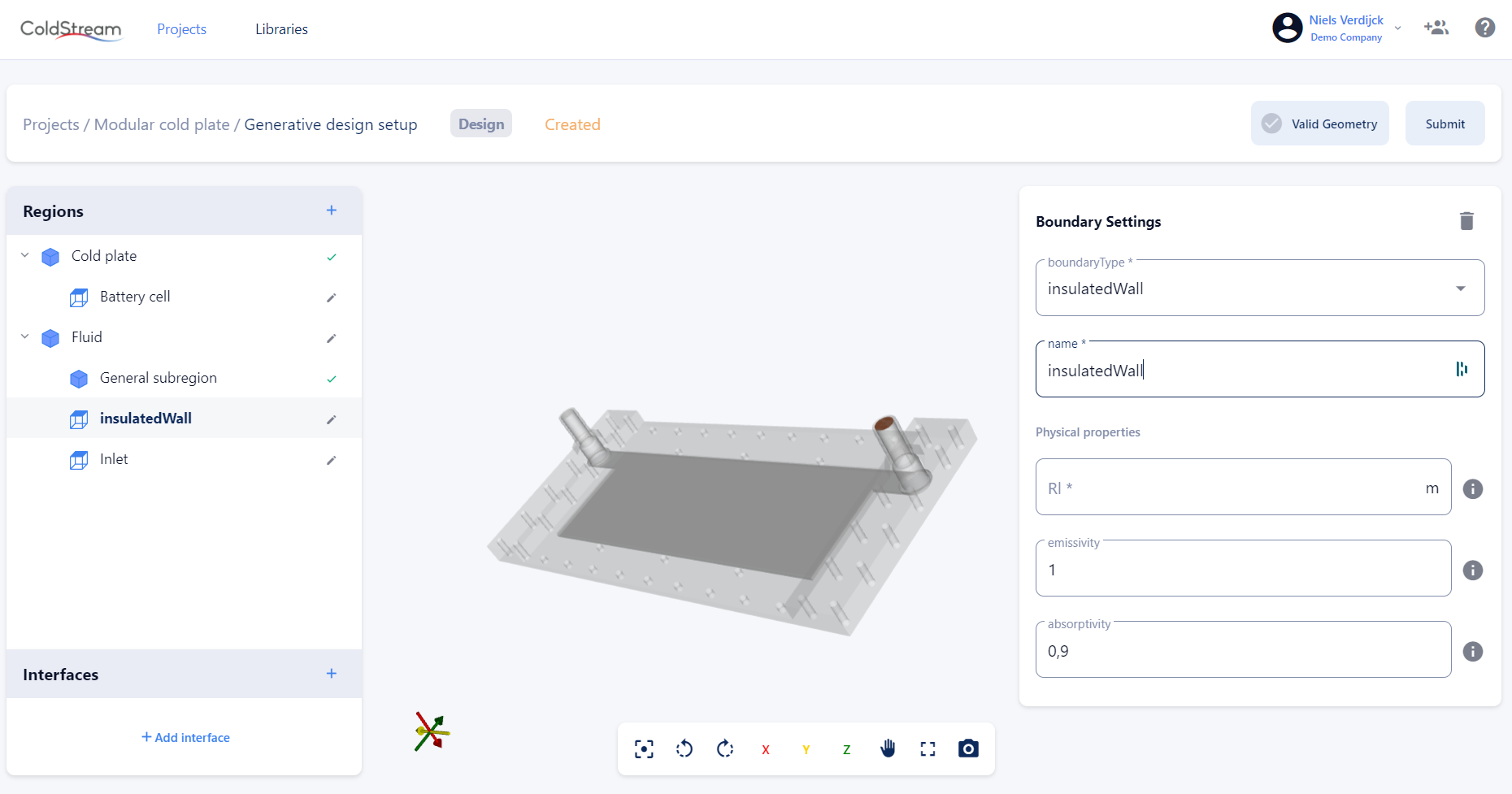
Input settings for an insulatedWall boundary
Note
Subregions of type 'general' and surface patches of type 'heatedWall' allow you to specify a localized heat input for your case.
Radiation
Introduction
For bodies with varying temperatures, energy exchange can occur in three modes: conduction, convection, and radiation. Conduction is the heat transfer by direct contact, convection is the heat transfer by motion of a fluid and radiation is the transfer of energy with the help of electromagnetic waves. In this article, we take a deeper look at radiative heat transfer.
Electromagnetic radiation is emitted by heated surfaces. This means all materials with an absolute temperature above zero degrees Kelvin, radiate thermal energy. The hotter the object, the more it will radiate to its colder surroundings, and the more important it becomes to take radiative heat transfer into account in your simulations. Radiation distinguishes itself from conduction and convection as it does not necessarily need a medium to carry it. Radiation can thus occur through any transparent medium, either a fluid, a solid, or a vacuum.
In radiative heat transfer, the Stefan-Boltzmann law is a well-known formula that relates the heat flow rate emitted by or absorbed from an object to the fourth power of its absolute surface temperature.
Besides the temperature of the body, the rate at which a body radiates thermal radiation also depends on the surface properties. A surface with an emissivity of one is called a black body. A black body is an idealized object that would absorb all wavelengths of thermal radiation it would receive, without reflecting or transmitting any energy. Hence, it would completely absorb all light and appear black at low temperatures. However, black bodies don’t exist in real life, in reality, all objects are gray bodies. This means incident radiation on a surface is partly reflected, absorbed, and transmitted according to the surface properties. For gray surfaces, the following condition holds:
If a medium absorbs, emits, or scatters a thermal ray that passes through it, it is called a participating medium. The ray can lose energy through absorption and scattering away from the ray. However, energy can also be gained from radiative sources in the medium through emission and scattering towards the ray. If the medium does not absorb, emit, or scatter a thermal ray, the medium is called a non-participating medium.
The energy balance of the ray over an infinite layer of the medium, results in a differential equation, i.e. the radiative heat transfer equation (RTE). Within our software, the RTE is solved with the Finite Volume Discrete Ordinates Method or FvDOM model in short. This means the RTE is solved for a discrete number of finite solid angles. This model is the most comprehensive radiation model, which can be used for (semi-) transparent media and can account for scattering and wavelength-dependent transmission. Our model can handle both participating and non-participating media. In the first case, the RTE is coupled with the general energy equation for fluids or solids, and a source term is added to the energy equation to account for the radiative heat transfer, in the latter case the source term is zero.
When to enable radiation?
If large temperature differences are to be expected concerning the surroundings, radiative heat transfer will become important, since it is proportional to the fourth power of the temperature (difference). In such cases, radiation should be enabled. When the radiative heat transfer is expected to be small in comparison to the convective heat transfer, radiation should not be enabled; unless this specifically needs to be modeled.
Which parameters to set on the platform?
How to enable radiation?
- Enable radiation in the concerned region by checking the radiation checkbox in the region settings window.
- In the boundaries related to the region, specify the emmisivity and absorptivity parameters in the boundary settings window.
- If the region is a solid type, specify the absorption coefficient in the solid material properties.
When radiative heat transfer is to be included for a specific region and the medium of the region is considered to be participating (i.e. the medium absorbs, emits, or scatters a thermal ray as it passes through), you need to enable radiation in the concerning region by checking the radiation box. In addition, the following parameters need to be set in the boundary settings of the boundaries related to the concerning region. If the concerning region is a solid type, also a material parameter related to radiation can be set:
Parameter | Units | Explanation |
---|---|---|
Boundary settings | ||
| | The emissivity of the boundary. This is a dimensionless value between 0 and 1. If no value is specified, a default value of 0.9 is adopted. |
| | The emissivity of the boundary. This is a dimensionless value between 0 and 1. If no value is specified, a default value of 0.9 is adopted. |
Solid material parameter setings | ||
| | The absorption coefficient represents the attenuation of the radiation intensity. |
On the boundaries, emissivity and absorptivity should be specified. The emissivity depends on the material of the surface and measures the capability to emit radiation. It is a representation of the ratio of energy radiated by the material to the energy radiated by a black body at the same temperature. The emissivity is considered constant for a given material. In reality, the emissivity depends on the wavelength of the radiation that is being emitted. However, in CFD models, the total emissivity is specified which is an integrated emissivity over all wavelengths. The emissivity of a surface is bound between 0 and 1. A perfect mirror, for example, would reflect all energy, hence the emissivity, and by Kirchhoff’s law, the absorptivity is zero. Within our software, the default value is set to 0.9.
The absorptivity is a dimensionless value between 0 and 1. If nothing is specified, the same value as the emissivity is taken by default.
When dealing with participating media in a simulation, some additional parameters need to be set. Since part of the radiative heat transfer can be absorbed in this case, leading to a change in radiation intensity, an absorption length should also be specified which represents the attenuation of the radiation intensity.
Turbulence
Introduction
In fluid dynamics, flow can be either laminar or turbulent. In the first case, the fluid particles follow a smooth path with almost no mixing or disruption between adjacent paths. On the other hand, in turbulent flow, the flow becomes very irregular and time dependent, and the fluid particles follow a chaotic path, full of eddies, swirls, and flow instabilities.
Turbulent flows are common in real life, think for example of the blood flow in your veins, the airflow over the wing of a plane, and breaking waves at the beach, ….
In the 19th century, Osborne Reynolds was one of the first scientists to perform a set of experiments and show the transition between laminar and turbulent flow regimes and to link this transition to the ratio of the inertial and the viscous forces.
This Reynolds number is still widely used today to characterize flow regimes. When the Reynolds number is smaller than 2300 in circular tubes, a laminar flow regime will occur. If the Reynolds number is higher than 4000, the flow will be turbulent. Everything in between is called the transitional regime.
When running simulations with turbulent flow, the turbulence needs to be resolved or an appropriate model needs to be selected. Turbulence models are simplified constitutive equations that predict the evolution of the turbulent flow. Even though a lot of research has been done over the past decades, turbulence modeling is still not a trivial task.
The difference between DNS, LES, RANS
To predict the evolution of the turbulent flow, three main approaches can be distinguished: DNS, LES, and RANS.
DNS
Turbulence can be fully described and resolved by the complete unsteady Navier-Stokes equations without the use of any modeling assumption regarding turbulence. This is called DNS, and stands for Direct Numerical Simulation. However, DNS requires extreme computational resources, because the mesh resolution and the time steps need to be extremely small in order to capture the full range of temporal and spatial scales. This makes the DNS approach impractical in industrial applications and is mainly considered as a research tool.
LES
In the Large Eddy Simulation approach, or LES in short, the most energy-containing structures of the flow, i.e. the large eddies are still resolved. Smaller scales of turbulence are treated by turbulence models instead.
RANS
The RANS, or the Reynolds-Averaged Navier-Stokes approach is the most commonly used approach in industrial applications. In most engineering applications, we are only interested in mean or integral quantities and to obtain these, solving turbulent flow with a turbulence model is the most cost-effective way to obtain adequate results. In this approach, the Navier-Stokes equations are averaged to obtain the mean equations of the fluid flow. These averaged equations are similar to the full Navier-Stokes equations but contain some additional terms in the momentum equation called the Reynolds stresses, stemming from to the nonlinearity of the equations. These Reynolds stresses are unknown and need to be modeled with a turbulence model.
There are a lot of different RANS models available, only the most common models are described on in more detail. Each of these models has its specific limitations based on their modeling assumptions.
model
RNG model
LaunderSharma model
model
SST model
Which model to choose in your application?
The selection of the turbulence model is important. Based on our experience, we can make the following recommendations.
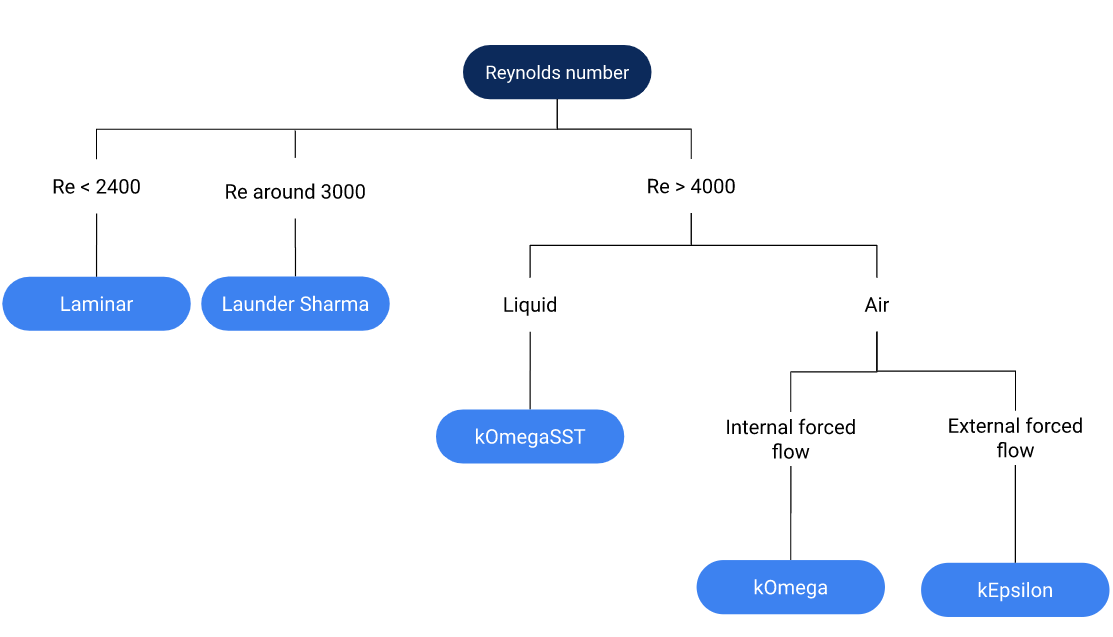
Turbulence model selection chart
First, the Reynolds number of the flow should be estimated. This Reynolds number is requiredo be estimated to determine whether or not your case is turbulent. It is acceptable to make assumptions and simplifications regarding the geometry or parameters.
So for a simple pipe or tube, the hydraulic diameter is equal to the diameter of the duct or pipe. Calculating the Reynolds number as previously defined, leads to:
From which can be determined, the flow can be considered turbulent. If you don’t know what the Reynolds number would be for your case and find it difficult to calculate, it is probably turbulent (Re>4000). If you have a case with very small parallel channels and a low velocity, chances are high that your case will be laminar.
With the Reynolds number determined, an appropriate turbulence model can be selected. If this Reynolds number is very low (Re < 2400) a laminar model should be selected.
If you expect your flow to be in the transitional regime, i.e. a Reynolds number around 3000, the best choice according to our experience is the LaunderSharma model as this model is appropriate for low Reynolds simulations.
References
- V. Yakhot, S.A. Orszag, S. Thangam, and C.G. Speziale. Development of Turbulence Models for Shear Flows by a Double Expansion technique. Physics of Fluids A Fluid Dynamics, 4(7), 1992.
- B.E. Launder and B.I. Sharma. Application of the energy-dissipation model of turbulence to the calculation of flow near a spinning disc. Letters in heat and mass transfer, 1(2), 131-137, 1974.
- D.C. Wilcox. Turbulence modelling for CFD, 2, 103-217. 1998.
- F.R. Menter and T. Esch. Elements of Industrial Heat Transfer Prediction. 16th Brazilian Congress of Mechanical Engineering (COBEM), 2001.
Buoyancy
Introduction
Buoyancy is an upward directed force, exerted by a fluid, that opposes the weight of the partially or fully immersed object, which was first described by Archimedes more than 2000 years ago.
So let’s take a look at an example and assume we have a cylindrical object, completely submerged in a box of water. The water pressure increases linearly with the depth, so the water pressure at the bottom of the cylinder is larger than the water pressure at the top of the cylinder.
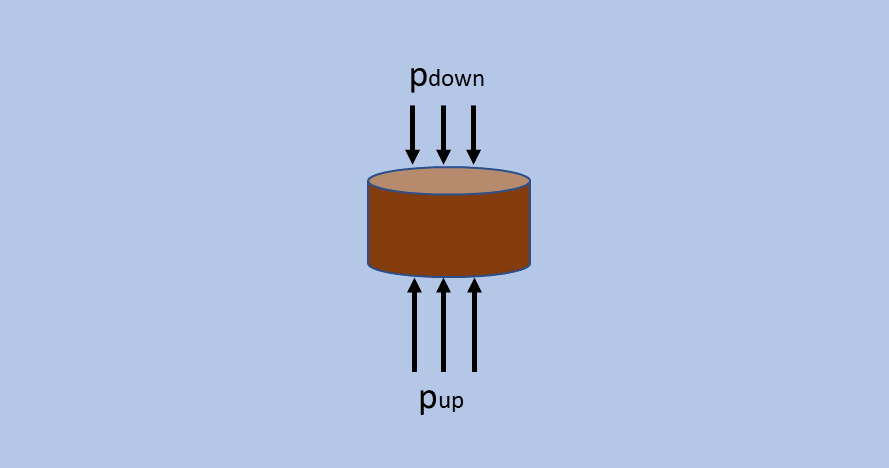
Buoyancy schematic
If we express this in terms of forces, we can say that the pressure difference will result in a net upward-directed force on the cylinder, which is called the buoyant force.
So the final equation becomes:
Hence the buoyancy force depends on the density of the fluid in which it is submerged, the gravity, and the volume of displaced fluid. This force is independent of the mass or the density of the submerged object. Furthermore, this force is also independent of how deep the object is in the fluid as the pressure at the top and the bottom of the object increases by the same amount if you go deeper.
- Sink when
- Remain in place when
- Rise upwards when and the object is fully submerged or floats when the object is only partially submerged.
An important example of when buoyancy is important is in natural convection cases, because in such cases the fluid motion occurs specifically due to buoyancy effects. When a heat source is added to the fluid, the density will vary with the temperature. The fluid will become less dense with increasing temperature and hot fluids will rise, triggering motion and flow. Buoyancy is also present in forced convection cases but is less dominant.
How buoyancy is taken into account on the platform
When the fluid density variation is limited, the density is modeled as a constant in the unsteady and convection terms and as a variable in the gravitational term. This method, the so-called Boussinesq approximation, is implemented in our software to account for buoyancy. The density which takes into account the thermal expansion is calculated as:
Which parameter to set on the platform
When buoyancy effects are to be included in a specific region, several parameters need to be set. These parameters are set in the region settings of the concerned region:
Parameter | Units | Explanation |
---|---|---|
| | The directional gravity vector. |
| | The thermal expansion coefficient needs to be set for the material that is assigned to the region. It can be specified as a constant value or as an array with the polynomial coefficients to include the temperature dependency. |
| | Optional: The initial temperature in the concerning region, serving as a
reference temperature. If nothing is specified, a temperature of 293.15 is set. |
| | Optional: The initial pressure in the concerning region, serving as a
reference pressure. If nothing is specified, a pressure of 1 (101325 ) is set. |
Rotation
Introduction
Rotation occurs in various engineering applications, such as turbomachinery (e.g. pumps, fans, turbines), rotating machinery (e.g., mixers, agitators), and automotive systems (e.g. wheels, gears). Understanding the flow dynamics around rotating components is crucial for optimizing performance, improving efficiency, and ensuring reliable operation.
In computational fluid dynamics (CFD) simulations, incorporating rotation can significantly enhance the accuracy and realism of the results, especially in scenarios involving rotating components. Rotation introduces complexities that must be appropriately accounted for in the simulation setup to ensure accurate predictions of flow behavior and heat transfer. This way, engineers can gain valuable insights into the effects of rotational motion on flow patterns, pressure distributions, and heat transfer phenomena.
How rotation is taken into account in ColdStream
In ColdStream, rotation is implemented using the Multiple Reference Frame (MRF) method. This method is a widely used approach for simulating flow around rotating components in CFD software. This method simplifies the computational domain by dividing it into stationary and rotating regions, allowing for efficient numerical solutions without explicitly resolving the motion of each rotating component.
In the MRF model, the computational domain is divided into multiple reference frames, each associated with a specific rotational speed and axis of rotation. The key principle behind the MRF method is to transform the governing equations from the absolute frame of reference to the relative frames, where the effects of rotation are accounted for through additional source terms in the momentum and energy equations. These source terms represent the centrifugal and Coriolis forces induced by rotation, enabling accurate prediction of flow behavior around rotating components.
Note
The MRF method is used in ColdStream to model rotation. This method divides the computational domain into multiple reference frames.
Important
The division of the computational domain into multiple reference frames is performed automatically by ColdStream in the background. There is no need to prepare an MRF zone in your CAD model.
Which parameters to set in ColdStream?
In the platform, the convention is to specify solid regions as rotating, and fluid regions as stationary. To enable rotation for a specific (solid) region, first click the “Add rotation” button in the “Region Settings”.
Then, you can specify the remaining inputs:
- The rotation axis direction: around which axis is the component rotating? (X, Y, or Z in the principal axis system
- The rotational velocity: how fast is the component rotating? [rad/s]
Important
Rotation should be enabled for each rotating region separately. Take care to ensure that the rotating region(s) are (predominantly) axisymmetric and will not intersect or overlap with other (solid) regions when they are rotated around their center of rotation.
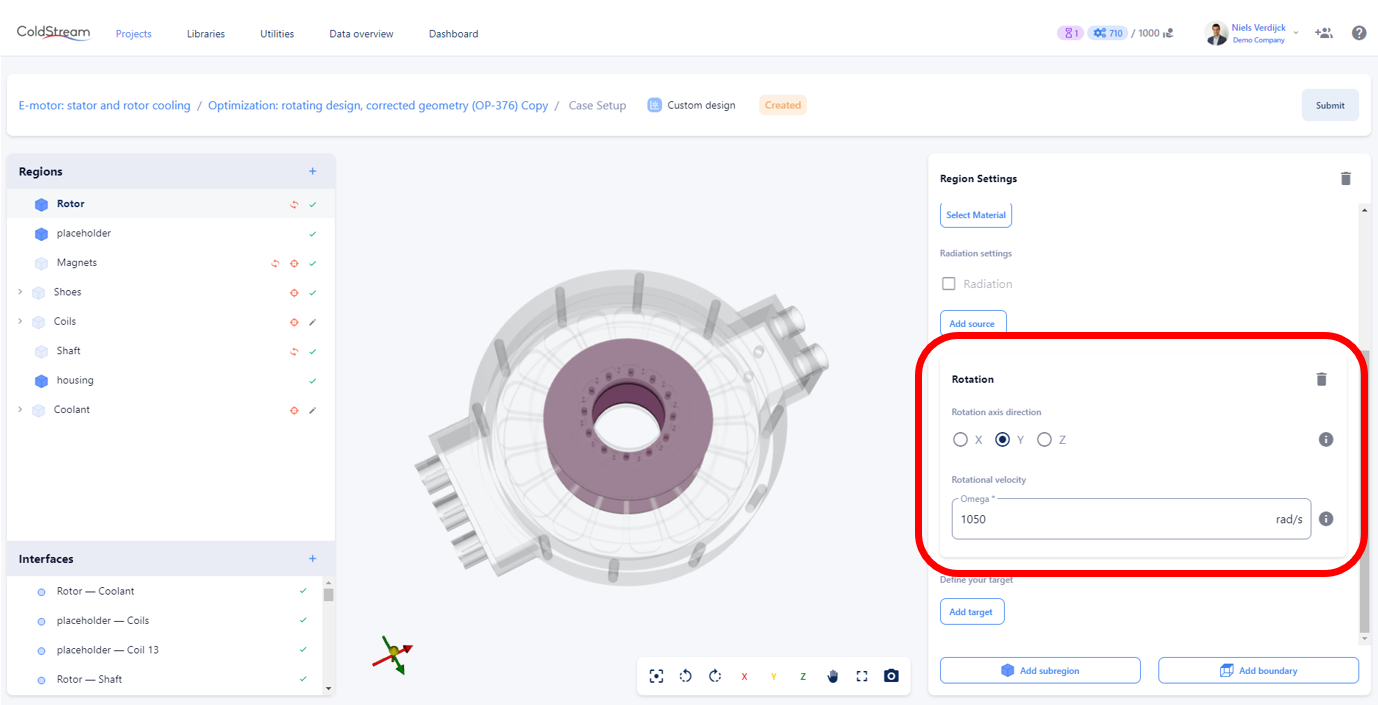
Input fields for rotation
Updated 8 months ago